I finally got around to taking pictures of  the samples from my 2 day collapse weave workshop with Anne Field. All I can say is WOW! I was just blown away with the technique!
It’s been three weeks since the workshop and my brain is still twitching with all the new possibilities. And this is one of the projects that I can’t seem to let go…
I am obsessed with this scarf of Anne’s. The brown stripes are handspun cashmere/silk. The white stripes are merino (commercially spun, I think). I don’t remember what the weft is, but I think it is wool/lycra. It is woven in 1/3, 3/1 reverse twill. The reverse twill in conjunction with the wool/lycra is what causes it to pleat up like this. High twist singles will behave similarly.
In fact, I already finished spinning some Spirit Trail Fiberworks cashmere/silk into a lace weight 2-ply for this scarf. I’m still trying to decide what yarn to use for the white — a wool/silk, 100% silk, or 100% wool. Then there’s the weft. I bought some cashmere/lycra from ColourMart that will do, but I’m could also use some hand spun singles. The effects, while similar, are slightly different. (More on this in the samples below.)
So, back to the workshop samples. I have 9 samples. Instead of overloading the front page with all the photos, I will put them “below the line.” Â Expand to see the rest of this post.
The set up…
A few weeks before the workshop, I received a little package in the mail from the workshop organizers. The package included a 15′ long warp chain of alternating 110/3 and 40/1 wool (1″ stripes). The 40/1 wool is so fine that you almost need magnifying glass to see! The instructions were for warping back to front.
I haven’t warped back to front in over 10 years. I just didn’t want to put the ultra fine singles through the reed/heddles twice (that’s what happens if you warp front to back). That’s just asking for trouble. So I bit the bullet and read Peggy Osterkamp’s book on warping several times. I built myself a raddle with 1/2″ spacing. And re-read Peggy’s book. Took several long breaths. And procrastinated until the day before the workshop.
It really wasn’t that bad. I’m not sure that I would do back to front too often. I find it fiddly. But it might be because I haven’t done it enough to be comfortable yet. Most of my projects right now are less than 4-5 yards, which is completely within the comfort zone for front to back. I can definitely see where it would be good for longer warps and/or more delicate warps.
And in case you are wondering, it took me about 5-6 hours to warp the loom. Not too bad. That part of it usually takes me about 3-4 hours front to back. This one has the extra complexity of those high twist singles. While it was mostly “at rest,” it still wanted to wrap itself up with the surrounding warp threads.
The yarns used:
In addition to the 110/3 and 40/1, Anne provided a selection of wool/lycra & cotton/lycra yarn to play with as warp. the 40/1 is most likely spun S.
But I couldn’t leave it at that. I pulled out some cormo and merino roving from my stash (processed by Morro Fleece Works) and created some S & Z spun singles. S singles are Cormo (light color), Z are MerinoX (dark brown). I wasn’t able to spin the merino nearly as fine as the cormo. I’m not sure why, but spinning it at 1AM may have something to do with it. Â The cormo was close to the 40/1 in diameter. The merino was somewhat fatter. (These are used in samples 5-9.)
The Samples:
Now onto the samples. Click on the images for full size. I do recommend it for the details. These pictures do not do these samples justice. They really need to be touched and stretched and oohed and aahed over. (You may need to click twice. Once to bring it up in its own screen, and again to enlarge.)
All samples are woven at 16 ppi (picks per inch) unless otherwise noted.
The top samples (grey towel background) are as they came off the loom, before finishing. The bottom samples (light background) are after they took a dip in hot soapy water. No other finishing (did not full, did not press). Just rolled up in a towel, squeezed dry, and passed a hair dryer of them to finish.
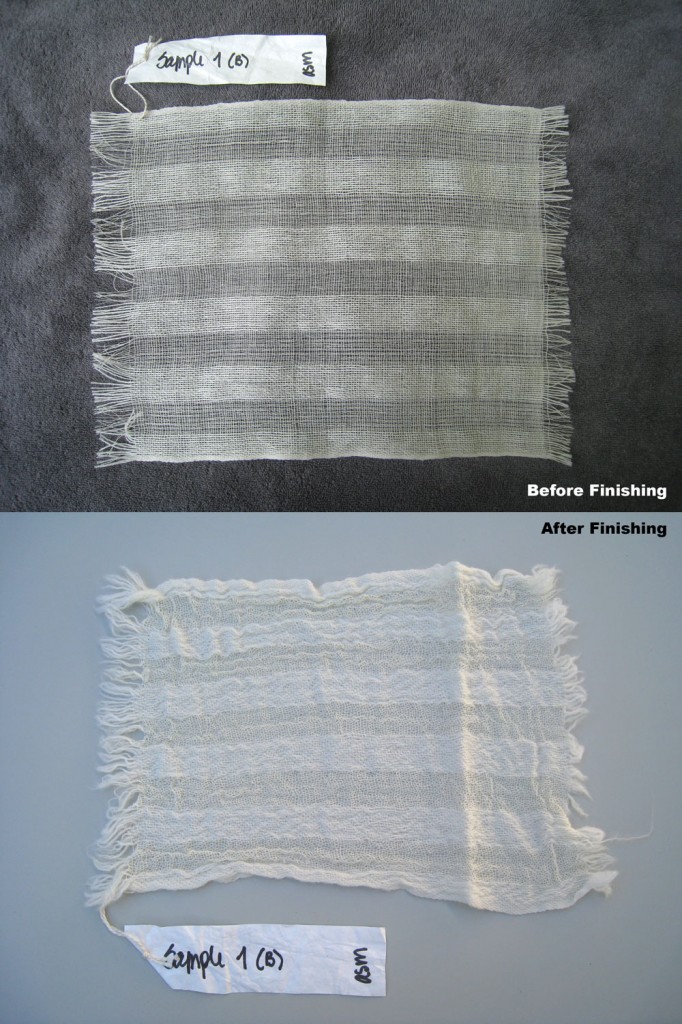
Sample 1: Plain weave with 40/1. See how the 40/1 "crinkled" up? See Sample 4 for how differently wool/lycra behaves.
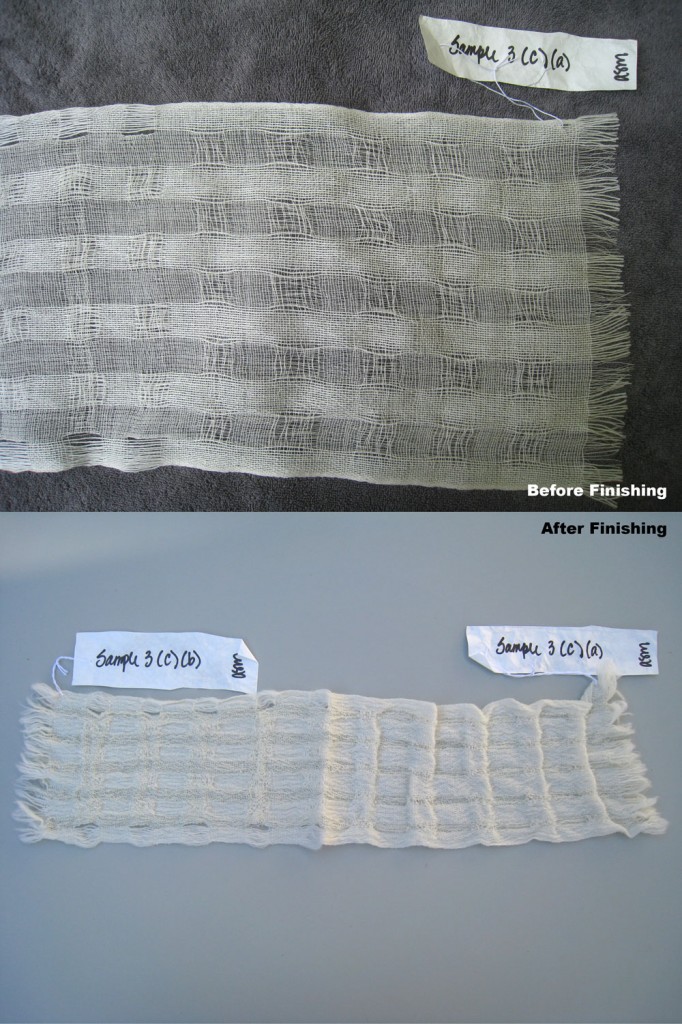
Sample 3: Plain weave. Both sides are alternating 1" blocks of 40/1 and wool/lycra, but...On the right, in addition to switching yarns, we also alternated 1" blocks of weaving across the full width and only over the 110/3 warp stripes (skipped the 40/1 stripes). Because the 40/1 warp collapsed on itself without the weft to support it, it produced the horizontal (on the loom) pleats. On the left, alternated 1" blocks on plain weave over all 11 stripes and just on the 40/1 (skipped the 110/3 stripes). No pleating here because the 110/3 did not collapse.
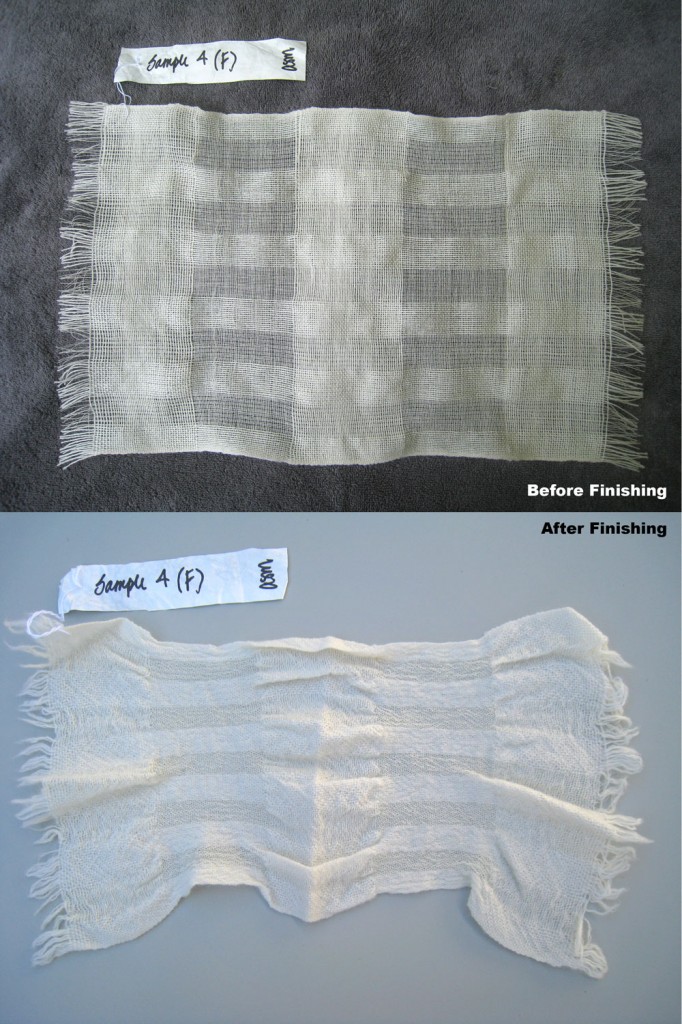
Sample 4: Plain Weave. Alternating 3" blocks of 110/3 and wool/lycra. This is the first time that you can really see the details on the wool/lycra. See how neat and tidy that drew in, as compared to Samples 1 & 2?
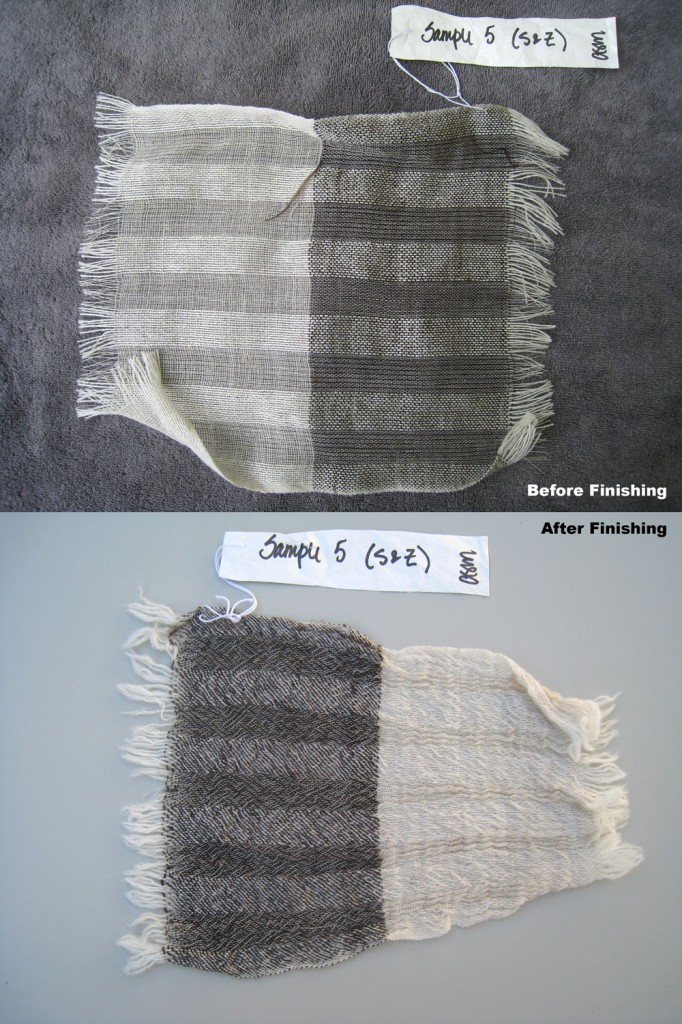
Sample 5: Plain weave using S (light) & Z (brown) spun singles. The tracking is really obvious in the brown section because of the contrast. Close examination of the light colored side also shows tracking.
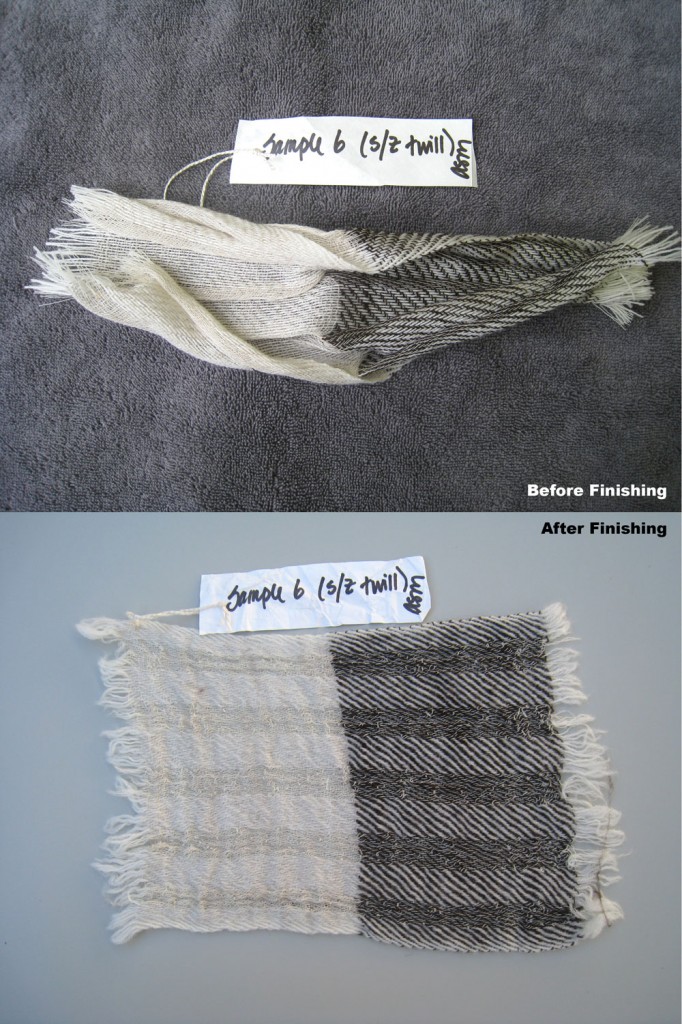
Sample 6: 2/2 twill with S & Z singles. Because of the twill and the active twist in the singles, the sample just immediately curled up when I cut it off the loom. It behaved better after a wash, most likely because it was laid flat and pressed in the towel in the correct aspect.
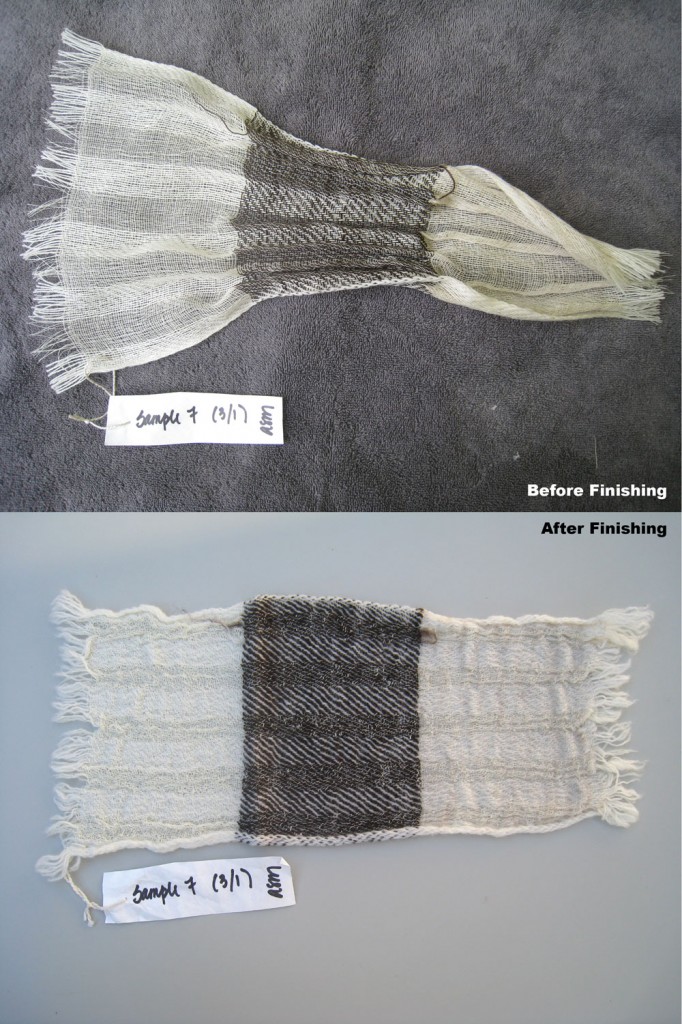
Sample 7: 2/2 twill. Left to right: 40/1, Z single, S single. I wanted to see how my singles compared with the commercially spun 40/1 singles. As you can see my S (far right) collapsed more than the 40/1. In handling, it has a lot more bounce too. It's likely that I put a lot more twist in my singles. The cormo has a much softer hand.
This is just a sample sample of things that can be done with collapse weave. My brain just wouldn’t stop spinning at all the possibilities. In fact, I signed up for the energized singles workshop with Kathryn Alexander at SOAR this year just so I can pick her brain on this. And Anne is working on an advanced collapse weave class for next year. I can’t wait!